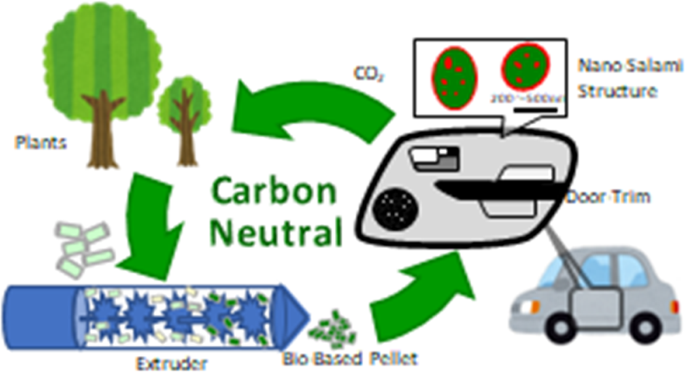
- Select a language for the TTS:
- UK English Female
- UK English Male
- US English Female
- US English Male
- Australian Female
- Australian Male
- Language selected: (auto detect) - EN
Play all audios:
ABSTRACT Polyamide 11 (PA11), a 100% biobased plastic derived from inedible plants, and polypropylene (PP) were mixed with a reactive compatibilizer using a twin-screw extruder. The
mechanical properties and morphology of the resulting injection-molded PP/PA11 bioalloys were investigated by flexural tests, Charpy notched impact tests, field-emission scanning electron
microscopy (FE-SEM), and transmission electron microscopy (TEM), among other tests. We found that it was possible to control the morphology of the bioalloy and that it had a wide range of
mechanical properties depending on the morphology. When the morphology of the bioalloy was a “ nanosalami” structure, as revealed by FE-SEM, the material had a Charpy notched impact strength
of 70–85 kJ/m2, which is superior to that of polycarbonates, without a large reduction in the flexural modulus. TEM observations showed that the reactive compatibilizers were located in the
interphase between the matrix and dispersed phase. The compatibilizers played a key role in improving impact strength. The bioalloy could be used for foam injection molding; therefore, it
was able to be applied as a foamed door trim, resulting in an approximately 30% weight reduction for the plastic part. Access through your institution Buy or subscribe This is a preview of
subscription content, access via your institution ACCESS OPTIONS Access through your institution Subscribe to this journal Receive 12 print issues and online access $259.00 per year only
$21.58 per issue Learn more Buy this article * Purchase on SpringerLink * Instant access to full article PDF Buy now Prices may be subject to local taxes which are calculated during checkout
ADDITIONAL ACCESS OPTIONS: * Log in * Learn about institutional subscriptions * Read our FAQs * Contact customer support SIMILAR CONTENT BEING VIEWED BY OTHERS SUSTAINABLE DEVELOPMENT OF
BIOEPOXY COMPOSITES REINFORCED WITH RECYCLED RIGID POLYURETHANE FOAM FOR MECHANICAL, THERMAL, ACOUSTIC, AND ELECTROMAGNETIC APPLICATIONS IN A CIRCULAR ECONOMY APPROACH Article Open access 10
March 2025 PERFORMANCE OF GLASS FIBER REINFORCED POLYAMIDE COMPOSITES EXPOSED TO BIOETHANOL FUEL AT HIGH TEMPERATURE Article Open access 19 August 2022 PENTADECAFLUOROOCTANOIC-ACID-FREE
POLYTETRAFLUOROETHYLENE AND MECHANISM OF PFOA FORMATION BY Γ-IRRADIATION Article Open access 18 August 2020 REFERENCES * MacArthur E. Beyond plastic waste. Science 2017;358:843. Article CAS
PubMed Google Scholar * https://www.undp.org/united-states/sustainable-development-goals. Accessed 31 Aug 2022. *
https://global.toyota/en/sustainability/esg/challenge2050/?_ga=2.54814819.95233906.1661070302-695201248.1658734777. Accessed 31 Aug 2022. * Lim LT, Auras R, Rubino M. Processing technologies
for poly(lactic acid). Prog Polym Sci. 2008;33:820–2. Article CAS Google Scholar * Nampoothiri KM, Nair NR, John RP. An overview of the recent developments in polylactide (PLA) research.
Bioresour Technol. 2010;101:8493–501. Article Google Scholar * Lenz RW, Marchessault RH. Bacterial polyesters: Biosynthesis, biodegradable plastics and biotechnology. Biomacromolecules
2005;6:1–8. Article CAS PubMed Google Scholar * Iwata T. Biodegradable and bio-based polymers: Future prospects of eco-friendly plastics. Angew Chem Int Ed. 2015;54:3210–5. Article CAS
Google Scholar * Lütke-Eversloh T, Fischer A, Remminghorst U, Kawada J, Marchessault RH, Boögershausen A, et al. Biosynthesis of novel thermoplastic polythioesters by engineered
Escherichia coli. Nat Mater. 2002;1:236–40. Article PubMed Google Scholar * Sano H, Usami T, Nakagawa H. Lamellar morphologies of melt-crystallized polyethylene, isotactic polypropylene
and ethylene-propylene copolymers by the Ru04 staining technique. Polymer 1986;27:1497–504. Article CAS Google Scholar * Kawada J, Kitou M, Mouri M, Mitsuoka T, Araki T, Lee CH, et al.
Morphology controlled PA11 bio-alloys with excellent impact strength. ACS Sustain. Chem Eng. 2016;4:2158–64. CAS Google Scholar * Donald AM, Kramer EJ. Craze initiation and growth in
high-impact polystyrene. J Appl Polym Sci. 1982;27:3729–41. Article CAS Google Scholar * Fischer M, Hellmann GP. On the evolution of phase patterns during the high-impact-modified
polystyrene process. Macromolecules 1996;29:2498–509. Article CAS Google Scholar * Kawada J, Kitou M, Mouri M, Kato Y, Katagiri Y, Matsushita M, et al. Super impact absorbing bio-alloys
from inedible plants. Green Chem. 2017;19:4503–8. Article CAS Google Scholar * Ide F, Hasegawa A. Studies on polymer blend of nylon 6 and polypropylene or nylon 6 and polystyrene using
the reaction polymer. J Appl Polym Sci. 1974;18:963–74. Article CAS Google Scholar * Gupta AK, Purwar SN. Crystallization of PP in PP/SEBS blends and its correlation with tensile
properties. J Appl Polym Sci. 1984;29:1595–609. Article CAS Google Scholar * Wu S. Phase structure and adhesion in polymer blends: A criterion for rubber toughening. Polymer
1985;26:1855–63. Article CAS Google Scholar * Wu S. A generalized criterion for rubber toughening: The critical matrix ligament thickness. J Appl Polym Sci. 1988;35:549–61. Article CAS
Google Scholar * Wu S. Chain structure, phase morphology, and toughness relationships in polymers and blends. Polym Eng Sci. 1990;30:753–61. Article CAS Google Scholar * Muratoglu OK,
Argon AS, Cohen RE, Weinberg M. Toughening mechanism of rubber-modified polyamides. Polymer 1995;36:921–30. Article CAS Google Scholar *
https://www.chemistryworld.com/news/castable-polymers-made-from-castor-beans/3007982.article. Accessed 31 Aug 2022. * https://www.toyota-boshoku.com/global/news/6783.html. Accessed 31 Aug
2022. Download references ACKNOWLEDGEMENTS The authors are grateful to Dr. Arimitsu Usuki and Mr. Osamu Kitou for their enormous guidance, strong encouragement, and continuous support.
AUTHOR INFORMATION AUTHORS AND AFFILIATIONS * Toyota Central R&D laboratories, Inc., 41-1 Yokomichi, Nagakute, Aichi, 480-1192, Japan Jumpei Kawada & Makoto Mouri * Toyota Boshoku
Corporation, 88 Kanayama, Kamekubi, Toyota, Aichi, 470-0395, Japan Masayuki Kitou, Toshiyuki Ario & Keisuke Kato Authors * Jumpei Kawada View author publications You can also search for
this author inPubMed Google Scholar * Masayuki Kitou View author publications You can also search for this author inPubMed Google Scholar * Makoto Mouri View author publications You can also
search for this author inPubMed Google Scholar * Toshiyuki Ario View author publications You can also search for this author inPubMed Google Scholar * Keisuke Kato View author publications
You can also search for this author inPubMed Google Scholar CORRESPONDING AUTHOR Correspondence to Jumpei Kawada. ETHICS DECLARATIONS CONFLICT OF INTEREST The authors declare no competing
interests. ADDITIONAL INFORMATION PUBLISHER’S NOTE Springer Nature remains neutral with regard to jurisdictional claims in published maps and institutional affiliations. RIGHTS AND
PERMISSIONS Springer Nature or its licensor (e.g. a society or other partner) holds exclusive rights to this article under a publishing agreement with the author(s) or other rightsholder(s);
author self-archiving of the accepted manuscript version of this article is solely governed by the terms of such publishing agreement and applicable law. Reprints and permissions ABOUT THIS
ARTICLE CITE THIS ARTICLE Kawada, J., Kitou, M., Mouri, M. _et al._ Invention of biobased polymer alloys and their application in plastic automobile parts. _Polym J_ 55, 753–760 (2023).
https://doi.org/10.1038/s41428-023-00760-1 Download citation * Received: 21 September 2022 * Revised: 09 January 2023 * Accepted: 11 January 2023 * Published: 16 March 2023 * Issue Date:
July 2023 * DOI: https://doi.org/10.1038/s41428-023-00760-1 SHARE THIS ARTICLE Anyone you share the following link with will be able to read this content: Get shareable link Sorry, a
shareable link is not currently available for this article. Copy to clipboard Provided by the Springer Nature SharedIt content-sharing initiative