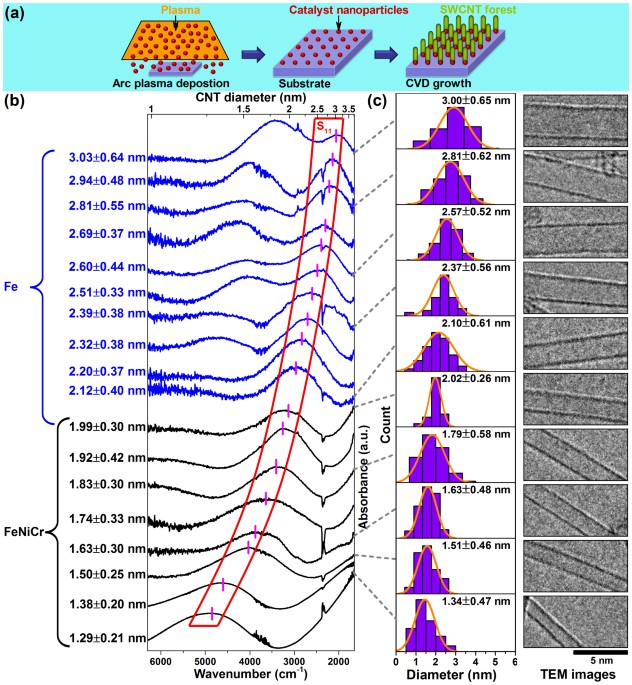
- Select a language for the TTS:
- UK English Female
- UK English Male
- US English Female
- US English Male
- Australian Female
- Australian Male
- Language selected: (auto detect) - EN
Play all audios:
We present a method to both precisely and continuously control the average diameter of single-walled carbon nanotubes in a forest ranging from 1.3 to 3.0 nm with ~1 Å resolution. The
diameter control of the forest was achieved through tuning of the catalyst state (size, density and composition) using arc plasma deposition of nanoparticles. This 1.7 nm control range and 1
Å precision exceed the highest reports to date.
For single-walled carbon nanotubes (SWCNTs), the diameter represents a critical structural aspect as it determines many electronic and chemical properties. For instance, diameter determines
the metallicity due to the inverse proportionality with the band gap1. Similarly, thermal properties are also dictated by the diameter as curvature is related with Umklapp scattering2.
Finally, diameter determines the radius of curvature of the tube which affects surface functionalization3. Therefore, diameter represents an important structural parameter of SWCNTs;
however, precise control of the SWCNT diameter over a wide range has yet to be demonstrated.
Previous results for the SWCNT diameter control can be grouped into two techniques: (1) floating catalyst method, where the SWCNTs are grown from catalysts flowing through a reactor tube and
(2) substrate growth, where the SWCNTs are grown from catalysts deposited onto a substrate. From our survey of previous reports, the floating catalyst method has demonstrated the widest
range of SWCNT diameter control with the highest precision, particularly in the smaller diameter range (~