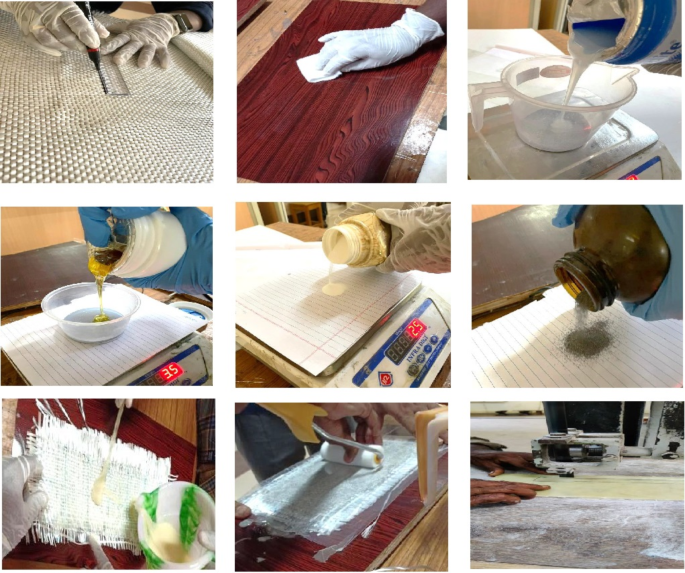
- Select a language for the TTS:
- UK English Female
- UK English Male
- US English Female
- US English Male
- Australian Female
- Australian Male
- Language selected: (auto detect) - EN
Play all audios:
ABSTRACT The work evaluated the usage of various filler materials, namely aluminium oxide (Al2O3), magnesium (Mg), and glass powder, in the bidirectional glass fibre reinforced polymer
(GFRP) composites. The required samples were fabricated using the hand lay-up technique by varying the filler material proportions from 0%wt. to 7.5%wt., including individual and hybrid
mixture combinations. The prepared samples were evaluated for their microhardness, tensile strength, deflection characteristics, and drop-weight impact resistance. It was observed that the
optimal addition of individual filler material improved the microhardness and tensile strength more than that of neat composites. In contrast, hybrid compositions at higher proportions
exhibited brittleness and lower enactment due to their poor interfacial bonding and particle agglomerations. The deflection characteristics and drop-weight impact tests also showed enhanced
stiffness and impact resistance with the addition of hybrid mixtures of filler materials to the composites. The study supports the potential use of adding filler materials to the composites
for lightweight structural applications. SIMILAR CONTENT BEING VIEWED BY OTHERS INFLUENCE OF DESIGNATED PROPERTIES ON THE CHARACTERISTICS OF DOMBEYA BUETTNERI FIBER/GRAPHITE HYBRID
REINFORCED POLYPROPYLENE COMPOSITES Article Open access 06 July 2020 EFFECTS OF WATER ABSORPTION ON THE MECHANICAL PROPERTIES OF HYBRID NATURAL FIBRE/PHENOL FORMALDEHYDE COMPOSITES Article
Open access 28 June 2021 FABRICATION OF GLASS/MADAR FIBERS REINFORCED HYBRID EPOXY COMPOSITE: A COMPREHENSIVE STUDY ON THE MATERIAL STABILITY Article Open access 10 April 2024 INTRODUCTION
Glass fibre reinforced polymer (GFRP) composites are valued for their potential strength-to-weight ratio, which supports lightweight structural constructions1. They also show good corrosion
resistance and chemical degradation compared to aluminium and steel materials2. They have the flexibility and design versatility to get moulded into required shapes, which helps in
developing complex structural prototypes. Even though the initial set-up and making cost of GFRP composites were found to be comparatively higher than traditional materials, its
cost-effectiveness at longer duration and reduced maintenance costs make it a suitable alternative3,4. The GFRP composites are affected by lower interlaminar shear strength, lesser thermal
resistance, inherent brittle nature, degradation, porosity, and low fatigue resistance, which can be overcome using filler materials5. Kumar et al.6 examined the individual usage of coal and
fly ash as filler materials in the GFRP matrix, a sustainable way to use industrial waste. The samples with 10% wt. coal ash and 15% wt. fly ash exhibited better tensile and flexural
strengths and impact resistance due to fine particle size and better interfacial bonding. The increase in the percentage of filler material reduced the strength due to void formation and
agglomeration. Zhang et al.7 investigated the use of glass beads as individual filler material with a diameter of 45 μm added to the polypropylene composites and compared their mechanical
strengths. A reduction in strength was observed due to the insufficient interface bonding of glass bead–polypropylene, which leads to prior cracking and more stress concentration points.
Glass powder as filler materials may reverse the adverse effects and improve the interface bonding. Petersen et al.8 conducted experiments with GFRP composites using alumina trihydrate (ATH)
as filler material and evaluated the compression, shear, tension, and flexural behaviour of the samples. The authors observed that the addition of ATH drastically reduced the strength of
the samples and made them brittle but still good enough to consider for fire-retardant structural applications. Jian et al.9 evaluated the mechanical strength of epoxy composites infused
with glass beads of diameter 100 μm and compared them with neat composites. The glass bead–infused composites were observed to have a reduced tensile strength for glass beads added above 15%
wt. due to the discontinuity of thermal expansion between the epoxy resin and glass beads. Reddy et al.10 examined the potential use of glass powder to infuse and use as filler material in
the GFRP composites. It was found that reinforcement with 5% wt. improved the tensile and flexural strengths by 18% and 26%, respectively, compared to neat composites. Further addition of
glass powder reduced the strength due to the fragility of glass powder and particle agglomeration. Aveen et al.11 manufactured samples of GFRP with individual filler materials, namely
titanium dioxide (TiO2), aluminium oxide (Al2O3), coal ash, fly ash, and silicon carbide (SiC), and tested the samples for their mechanical strengths. It was found that Al2O3 and TiO2 of
around 5% wt. showed better mechanical strength; further increase in concentrations reduced the strength due to particle agglomeration. Buaphuen et al.12 used broken and waste glass
materials as fillers in powder form at 0–5% wt. to prepare the GFRP composites. The addition of glass powder resulted in increased density compared to neat composites, which was also
observed in the increased microhardness of the sample. Vijaya Rajan and Gnanavel13 prepared GFRP composites by adding glass powder as filler materials in varying percentages (0–2%wt.) and
investigated their mechanical strength. It was observed that glass powder was added at concentrations between 0.5% wt. and 1.5% wt. showed better strength, which also led to a change in
failure mode from adhesive failure to cohesiveness. Further addition of glass powder caused localized stress concentrations and agglomeration at the epoxy–filler materials interfaces, which
led to quick failure. Zhang et al.14 carried out experiments with glass fibres as reinforcing material and magnesium silicate hydrate cement as a matrix element for preparing composite
samples. It was observed that adding 0.9% wt. glass fibre improved the compressive and flexural strengths and was seen with lesser crack propagation due to proper dispersion of glass fibre.
In contrast, further addition of glass fibre tends to agglomerate and tangle, decreasing the composites’ mechanical strength. Lugas Gada et al.15 prepared uni-directional GFRP composites and
used glass powders as filler materials at varying percentages from 0% wt. to 7.5% wt. to manufacture samples. They tested these samples for their physical and mechanical characteristics.
The addition of glass powder at an optimal concentration enhanced the flexural strength of the samples compared to neat composites due to interlaminar shear strength and interfacial
strengthening mechanism, further increasing the filler material, leading to void and micro-voids, which acted as a stress concentrator, and reducing the mechanical strength of the samples.
In a study by Zheng et al.16 used Al2O3 as filler material, glass fibre as reinforcement material, and epoxy resin as a matrix to evaluate its mechanical and thermal behaviour through
hand-paste moulding and vacuum processes. It was observed that the addition of 2% wt. of Al2O3 improved the mechanical behaviour, and 20% wt. increased thermal conductivity, combustion time,
and specific heat capacity. Daffa Alandro et al.17 used graphite fillers ranging from 0.5 to 2% wt. in manufacturing glass fibre-reinforced polymer composites. The study revealed that
composite infused with 0.5% wt. of graphite exhibited 16.94 MPa shear stress and 0.293 µε shear strain compared to pure composites with 8.06 MPa shear stress and 0.311 µε. The results
emphasize the potential use of fillers to enhance the mechanical performance of GFRP composites since they are observed to have more resistance to shear stress. In our previous experimental
work, the addition of 5% wt. Yttrium powder as filler material improved the tensile strength of the GFRP composites from 159 MPa (neat composite) to 223 MPa and improved the micro-hardness
from 2.39 Hv (neat composite) to 22.7 Hv18. Table 1 shows the summarized discussion and inference of various literature that are related to the addition of individual filler materials in
GFRP composites. Etika, K. C., et al.19 examined the use of carbon black particles of 42 nm and clay particles of 200 nm at hybrid concentrations between 0.05% and 0.1% wt. and evaluated the
mechanical and electrical properties of epoxy composites. The addition of 0.5% wt. clay increased the electrical conductivity but no improvement in the storage modulus. The equivalent
addition of carbon black and clay was observed with improved storage modules but decreased electrical conductivity, whereas the optimal addition of 1:2 clay and carbon black showed better
results for the electrical conductivity and storage modulus. Uddin, M. F., and Sun, C. T20. studied the integration of hybrid filler materials, aluminium oxide (Al2O3) 0–3%wt. silica 0–15%
wt. and carbon nano fibres 0-1.5%wt. The uniform dispersion of particles shows improvements in mechanical properties with the incremental particle loadings. The good dispersion of particles
would result in better mechanical properties and reduce particle agglomeration with the use of hybrid nanoparticles. Megahed, A. A. et al.21 investigated the use of silica (SiO2) and carbon
black (C) nanoparticles for the tribological performance of hybrid composites. The individual and hybrid addition showed improvements in the hardness and wear resistance of composites
compared to neat composites. At lower loads, the 1% wt. silica exhibited improved wear resistance, whereas at higher loads, 0.5% wt. silica and 0.5% wt. carbon black were observed to have
high weight loss in the wear test. Authors also suggested that silica nanoparticles and silica-based particles are more cost-effective than carbon nanoparticles as an economically viable
alternative. They also explored the usage of silica (SiO2) and carbon black (C) nanoparticles in the woven and nonwoven types of E-glass fibre-based composites. The addition of 0.5% wt. of
carbon black nanoparticles showed 19% and 60% improvement in its tensile strength and fatigue behaviour. Hybrid composites with 1%wt. observed with 57% improved tensile modules and 28%
improved impact strength compared to neat composites. The addition of 0.25%wt. SiO2 and 0.25% wt. of carbon black nanoparticles also showed better tensile and impact strengths compared to
neat composites22. Alam, M. S., and Chowdhury, M. A23. used calcium carbonate (Ca2CO3), aluminium oxide (Al2O3), magnesium oxide (MgO), titanium dioxide (TiO2), and copper oxide (CuO), on
the mechanical behaviour of composites of CaCO3-Al2O3-MgO-CuO at different weight ratios (5, 10 and 15 gm). A significant increase in tensile strength of 20.3%, flexural strength of 26.6%
and impact strength of 12.9% was observed for the composite made of CuO filler materials of TiO2 particles, and more particle agglomeration was observed in the usage of a hybrid combination
use of filler materials. The study by Wan Badaruzzaman et al.24 examined the water absorption capacity and mechanical properties of hybrid GFRP composites reinforced with woven E-glass
fabric, epoxy resin, kenaf, and coconut fibres, along with filler materials like fly ash, nano-silica, and calcium carbonate (CaCO3). The composites were prepared with 10% wt. CaCO3 and fly
ash displayed the highest tensile strength, while increased CaCO3 content improved compressive and flexural strength. The composites were prepared with 30% wt. GFRP, 50% wt. resin, 15% wt.
fly ash, and 5% wt. CaCO3 shows the lowest water absorption rate of 0.45%. The study determined that the combination of reinforcing materials and fillers (fly ash and CaCO3) improved both
mechanical performance and water resistance, which is suitable for structural applications in flood-affected areas. Zamani P. et al.25 explored the static strength, fatigue endurance, and
crack initiation life of aluminum-to-GFRP bonded joints under four-point bending and its synergistic effects of hybrid nanoparticle reinforcement using graphene nanoplatelets (GNP) and
silica nanoparticles (SNP). The proportions, namely 30% GNP + 70% SNP, 50% GNP + 50% SNP, and 70% GNP + 30% SNP, with 0.5, 1.0, and 1.5% wt. A high static failure was observed for 0.5 and
1.0%wt. of 70% GNP + 30% SNP, whereas 1.5% wt. with 30% GNP + 70% SNP gave better static results. SEM analysis exposed that GNP-dominant mechanisms, such as crack arrest and crack path
deviation at lower fatigue loads, while SNP-dominant mechanisms, like plastic void growth, enhanced crack initiation at higher loads. The study reveals that hybrid reinforcement extends a
cost-effective solution, improving static strength, fatigue life, and crack initiation compared to single-type reinforcements. El-Masry, M. M., & Imam, N. G26. synthesized hybrid
nanocomposites using the coprecipitation method and examined with various characterization techniques. The integration of Ag-CuO and Mg-CuO nanofillers substantially improved the physical
and chemical characteristics of neat epoxy composites. The use of Ag-CuO nanoparticles enhances thermal stability, dielectric properties and electrical conductivity and is observed to be a
low-cost applicant for electronic applications. The use of Mg-CuO nanosheets exposed good ductility and a wider elastic range to the epoxy matrix. The Ag-CuO/Epoxy composites exhibited up to
seven times greater thermal stability compared to neat epoxy composites, and Mg-CuO/Epoxy composites supported enhanced elasticity. Srinivasa Perumal, K et al.27 used ball-milled ilmenite
(FeTiO3) and silicon dioxide (SiO2) fillers (63 nm and 67.5 nm) and added to epoxy in varying proportions of 0:0, 2.5:2.5, 5:5, and 7.5:7.5% wt. The study observed 12.2%, 32.22%, 28.98%,
23.78%, and 4.65% improvement in tensile strength, tensile modulus, flexural strength, flexural modulus, elongations at break and “D” hardness value for the 5:5%wt. ratio of hybrid
filler-based composites compared to neat composites. Field emission scanning electron microscopy (FESEM) analysis exposed an effective interfacial bonding, reduced fibre pullout and uniform
filler dispersion for the hybrid configuration of fillers, which enhanced the mechanical, tribological, and structural properties of GFRP composites. Kumara R. et al.28 developed the
epoxy-based hybrid polymer composites employing the hand-lay technique, integrating E-glass fibre as a reinforcing material and Al2O3/SiC as filler materials at equal proportions. The
results show that the composite with 4%wt. of Al2O3/SiC exhibits a better tensile strength of 170.84 MPa and flexural strength of 162.56 MPa; further additions result in decreased
properties. Huseyin Kose et al.29 conducted an experiment using hybrid filler materials of copper oxide (CuO) and magnesium oxide (MgO) in nano-sized particles from 0 to 0.8%wt. added to the
GFRP composites to evaluate their tensile-tensile fatigue tests. It was observed that the hybrid addition of CuO and MgO nanoparticles improved the brittleness and stiffness of the GFRP
composites, respectively. Moreover, the use of hybrid nanoparticles has improved the fatigue life of the samples compared to individual use of nanoparticles. The results showed that the
addition of hybrid nanoparticles improved the fatigue life of GFRP composites for the combination of 0.6% wt. MgO & 0.4%wt. CuO and 0.2%wt. & MgO–0.6%wt. samples. The CuO composites
were observed to have the highest fatigue life of 39.5k and 13.7k cycles at 70% and 80% load levels, respectively. Table 2 shows the summarized discussion and inference of various literature
that are related to the addition of hybrid filler materials in GFRP composites. From the literature review, the GFRP composites are primarily known for their high strength-to-weight ratio
and corrosion resistance. In contrast, it endures limitations such as low brittleness, interlaminar shear strength and porosity, which can be moderated using filler materials. Common filler
materials in the form of micro or nano-sized particles such as coal ash, fly ash, glass beads, glass powders, TiO2, Al2O3, graphite, and yttrium have been used to enhance the mechanical,
thermal, and other performance aspects of GFRP composites. The addition of such individual filler materials was observed to improve the mechanical performance of the composites, whereas the
non-optimal addition leads to reduced strength. Further, researchers reported that the usage of hybrid filler materials, such as carbon black with clay, Al2O3 with silica, SiO2 with carbon
black, Ca2CO3, Al2O3, MgO, TiO2 and CuO, Graphene with silica, Ag-CuO, Mg-CuO, FeTiO3 with silica, CuO and MgO have shown promising improvements in mechanical properties, including enhanced
wear resistance, hardness, tensile strength, and fatigue life. Non-optimal addition of the hybrid filler materials was also observed as not enhancing the results due to various
microstructural damages, micro-porosity, particle agglomeration, and insufficient interfacial bonding in the fibre matrix. The previous studies have considerably explored the use of
aluminium oxide (Al2O3), magnesium (Mg), and glass in composite materials, which focused on using these materials as individual fillers. The synergistic effects of using these materials, as
well as the interaction between these materials and their collective impact when used as hybrid filler materials on mechanical, tribological, and thermal properties, were underexplored. The
authors aim to address the identified gap by exploring the individual and combined effects of Al2O3, Mg, and glass at varying proportions on their microhardness, tensile strength, stiffness
and drop-weight impact resistance with that of neat composites and provide a pathway for better composite material design. MATERIALS AND METHODS MATERIALS USED In this work, bidirectional
glass fibre–reinforced polymer (GFRP) mats with 0.4 mm thickness were purchased commercially (M/s New Era Composites, Chennai) and used as the base material. The standard epoxy resin
(Aralidte XIN 100) and hardener (XIN 900) are considered in the ratio of 2:1 with a volume fraction of 60:40 for the fibre resin. Polyvinyl coating was applied to the cardboard mould surface
to prevent adhesion after the curing of samples. The hand lay-up technique was considered for the preparation of glass epoxy composite samples. Aluminium oxide (Al2O3) of Brockmann activity
grade I with an average size of 150 μm, magnesium (Mg) with an average particle size of 450 μm (purchased from M/s. Royal Scientific), and glass powders of coarse grade with an average
particle size of 300 μm (purchased from M/s. Akshar Chem) are considered as filler materials. SAMPLE PREPARATION The required composition of resin, hardener, and filler materials was
considered as per the sample conditions listed in Table 3. The mass, density, and specific gravity values are assessed to find the volume fraction of each sample and maintain uniformity
among the various samples. The composition mixture was applied on the GFRP sheet one over the other, covering a total of six layers of sheets at ambient room temperature. A steel handle
roller made of polyurethane sponge foams was used to ensure the even distribution of the mixture during the hand lay-up technique and to remove any air bubbles for ensuring smooth lamination
of GFRP samples. The prepared samples (each of L = 300 mm, W = 150 mm, and t = 5 ± 0.3 mm) were kept in a tight fit with an upside-down cardboard mould and left for one day at the same
ambient temperature for the curing process. The next day, the samples were taken out of the mould and machined to the required size for various tests in accordance with the American Society
for Testing and Materials (ASTM) standards. Figure 1 shows the procedure followed for the sample preparation process. TESTING PROCEDURE MICROHARDNESS The microhardness of various samples was
tested in a Vicker’s hardness testing machine (make: Struers, model: Duramin-4, Denmark) as per the ASTM E384 with 500 g as load and 15 s as dwell time with an accuracy of ± 0.5 HV. The
load and dwell time were determined with a few random trials to observe proper indentation on the sample surfaces for its reliability and repeatability after calibration of the equipment.
Each sample was measured at three different locations (L1, L2, and L3), as marked in Fig. 2, and the average was considered for every sample. Table 4 presents the average microhardness
values observed across various samples. Figure 3 shows the sample under microhardness measurement. TENSILE TEST The tensile tests as per the ASTM D3039 standard, using the specified specimen
size and standard testing procedures, and adhered to the sample design in the Universal Testing Machine (UTM) (make: Tinius Olsen machine, USA). Following the curing process, the samples
were trimmed to the required size using a motorized vertical hack saw machine. Figure 4a–c shows the UTM machine set-up, a dimensional drawing to indicate the area considered for cutting the
sample to perform the tensile test, and the sample marked as per the ASTM standard. SCANNING ELECTRON MICROSCOPE (SEM) AND ENERGY DISPERSIVE X-RAY SPECTROSCOPY (EDAX) A composite sample was
sectioned into a specimen size of 10 mm × 10 mm (focused on the central region of the specimen after cutting out the other regions) to fit in the test set-up. Since the considered sample is
electrically non-conductive in nature, the sample was sputter-coated and placed on the aluminium stabs with conductive carbon tape pasted on the sample. The prepared samples were then
analysed in the SEM (make: JEOL JSM-7600, Japan) and in EDAX (make: Oxford Instruments, United Kingdom). The tensile fractured samples were examined in SEM (make: Exo 18, model: Carl Zeiss,
Germany). CUSTOM-BUILT DEFLECTION TEST An Indigenous deflection test set-up was employed using a calibrated standard weight and dial gauge set-up (least count = 0.01 mm), as shown in Fig. 5,
to assess the deflection of composite materials by subjecting the composite samples to bending force. Its deflections were measured; however, the fracture behaviour of the samples were not
considered. The specific samples of size of 300 mm × 25 mm × 1 mm (length, width, and thickness, respectively) were tested for deflection with variations in the load range between 20 g and
520 g by keeping the extremes of the set-up magnetically fixed to ensure stability during testing. The test set-up was developed and used to analyse the behaviour of the samples at low-load
testing, showing the potential of these composites for lightweight applications. VERTICAL IRON IMPACTOR DROP WEIGHT TEST The Indigenous vertical iron impactor drop test set-up was used to
assess the influence of specific filler materials on GFRP composites. A limited number of samples of size 100 mm × 100 mm were tested by free-falling of a 4 kg iron impactor with a diameter
of 25 mm at a velocity of 0.6 m/s from 60 cm height onto the samples kept on the bottom support as shown in Fig. 6. RESULTS AND DISCUSSION MICROHARDNESS The microhardness of the composite
samples (refer to Table 4) was assessed to understand the influence of Al2O3, Mg, glass powder, and fibre conditions. Figure 7 shows the average microhardness of various samples. The samples
with 5%wt. Al2O3 (constant) and varying Mg content exhibited an inconsistent correlation (S1–S4). Adding Mg content initially increased the microhardness (2.5%wt. Mg), but further addition
resulted in decreased microhardness. Similarly, the samples with 5%wt. Mg (constant) and varying Al2O3 content also displayed an inconsistent correlation (S5-S8). Further addition of Al2O3
resulted in decreased microhardness. The outcomes indicated that adding filler materials (Mg and Al2O3) notably improves the microhardness compared to the S14 neat composite. In contrast,
more than 2.5%wt. of the addition of either of the filler materials leads to a reduction due to the brittle phases and non-uniform distribution of filler materials during manufacturing. The
results indicated that both Mg and Al2O3 content significantly affect the microhardness of the composites. A moderate amount of Mg (2.5%wt.) and Al2O3 (2.5%wt.) tends to optimize the
microhardness, while higher concentrations lead to a reduction. This could be due to the formation of brittle phases or the non-uniform distribution of particles, which could generate weak
points and lose mechanical integrity at higher concentrations. The samples S9–S12 contain a constant addition of 6.5%wt. of glass powder as filler materials observed with significantly
higher microhardness compared to S1–S8; this indicates that the addition of glass powder in the glass epoxy composites enhances microhardness. The innate hardness of glass powder and its
inclusion, along with two filler materials, possibly helped to enhance the reinforcement with the effective distribution of particles and better interfacial bonding of filler materials with
the fibre sheet. The results were observed with the combined synergistic improvement of microhardness for the samples with glass powders as filler materials compared to other samples. The
richness in silicon, reinforcement effect, filling of the voids, better load transfer, resistance to wear, and indentation help the composites with glass powder improve their microhardness.
An additional experiment S13 was conducted using chopped GFRP sheets (the sheets were chopped into small pieces and added during sample preparation) to understand the reinforcement between
the filler materials and the fibre sheet. The random orientation of the chopped fibre reduced the microhardness due to uneven dispersion and weak interfacial bonding. Figure 8 shows the
average microhardness values of samples S1, S5, S9, S11, S13, and S14. Samples S1 (5.14 Hv) and S5 (6.99 Hv) were observed to have improved microhardness compared to the neat composite S14
(2.39 Hv). The presence of either Al2O3 or Mg powder was observed to show some individual synergetic effect when used as a filler in GFRP composites. Adding glass powder as filler material
also significantly increased microhardness, as observed in samples S9 and S11. Further, it was observed that an equal amount of Al2O3 and Mg powder added along with the glass powder to the
composite improved microhardness substantially (S11, 16.61 Hv). In contrast, sample S13 also observed higher values, but it cannot be considered further due to the presence of chopped
fibres, which may lead to unrealistic results for real-time applications. ELEMENTAL COMPOSITION USING EDAX Figure 9a,b shows a scanning electron microscopy (SEM) image with an associated
energy-dispersive X-ray spectroscopy (EDS) spectrum as spectrum 1 for sample S11 focused on an area of the composite sample without visible fibre presence. The carbon element (58.63%wt.) and
oxygen element (40.55%wt.) confirm the presence of epoxy resin and resin matrix, respectively (refer to Table 5). The presence of Mg (0.16%wt.) and Al (0.09%wt.) confirms the addition of Mg
and Al2O3, respectively, as filler materials in the sample. The other elements, namely Na (0.20%wt.) and Si (0.32%wt.), indicate the presence of soda-lime glass components, which confirms
the usage of glass powder in the composite specimen. Figure 10a,b shows a SEM image with an associated energy-dispersive X-ray spectroscopy (EDS) spectrum as spectrum 2 focused on an area of
the composite sample S11 with visible fibre presence. The SEM image in that region has more textured regions, possibly indicating areas with glass fibre presence or matrix–fibre interface.
The carbon element was observed to be high (43.29%wt.), which indicated the presence of epoxy resin, and the oxygen element was observed at 46.33%wt. (refer to Table 6), which is associated
with resin matrix and oxidation with other chemical elements during the sample preparation. The presence of Mg (0.52%wt.) and Al (0.91%wt.) confirms the addition of Mg and Al2O3,
respectively, as filler materials in the sample. The other elements, namely Si (2.73%wt.) and Ca (1.25%wt.), confirm that the composite material in that region has a significant amount of
glass content. The analysed region of spectrum 1 was observed to have more resin content with minimal reinforcement and filler materials, whereas spectrum 2 was observed to have a more
balanced composition of resin, fibre, and filler contents. TENSILE STRENGTH The tensile strength of the composite samples (refer to Table 7) was measured to understand the influence of
Al2O3, Mg, glass powder, and fibre conditions in various samples. Figure 11 shows the stress–strain curves for four different composite samples (S1, S2, S3, and S4) with varying amounts of
Mg while keeping Al2O3 constant at 5%wt. and no glass powder. All samples showed a typical ductile material behaviour with a clear linear elastic region followed by plastic deformation and
eventual fracture. Sample S1 had the highest UTS (236 MPa), showing that the absence of Mg leads to better tensile properties and was influenced by the properties of Al2O3 and GFRP fibres.
Adding Mg with varying concentrations declined the tensile strength of the samples (S2–S4) due to porosity or weaker interfacial bonding, reducing the material’s ability to withstand tensile
loads. The presence of Mg content alters the microstructure, forming Mg-rich phases and regions that are ineffective for the load-bearing capabilities and the interaction between Al2O3 and
Mg, leading to weaker composite structures. The composites become less ductile and more brittle with the presence of Mg, leading to reduced mechanical performance under tensile loads.
Forming derivative phases or porous and brittle intermetallic nature weakens matrix strength while increasing the filler content. Figure 12 shows the stress–strain curves for four different
composite samples (S5, S6, S7, and S8) with varying amounts of Al2O3, a constant amount of Mg (5%wt.), and no glass powder. The increasing content of Al2O3 alters the microstructure,
reducing the effectiveness of the load transfer between the matrix and the fibres and forming hard, brittle clusters. Even though Al2O3 may help in improving the strength of the matrix, a
higher amount leads to early failure due to particle agglomeration and weak points within the matrix, which support matrix discontinuity and reduced tensile strength. The composite becomes
more brittle and less capable of withstanding tensile stress, with the combination of 0%wt. Al2O3 and 5%wt. Mg (S5) providing the best mechanical performance among the samples tested
(S5–S8). Figure 13 shows the stress–strain curves for six different composite samples (S9–S14), in which S9–S12 were made with constant amounts of Al2O3 and glass powder by varying the Mg
powder concentrations. The increase in Mg content from 2.5%wt. to 7.5%wt. decreased the tensile strength, similar to the previous set of samples (S1–S4), indicating that Mg does not
synergize well with the other composite materials, potentially reducing the material’s stiffness or leading to weaker interfaces. In addition, an experiment using chopped fibres (S13) was
performed to understand the role and behaviour of fibre. The strength was drastically reduced and was not in line with the fibre sheet due to the location, orientation, and length of the
chopped fibres, which were the reason for the load-bearing behaviour of the sample. The overall results of the tensile tests show that the addition of Al2O3 improves the composite’s
performance, while Mg has a detrimental effect compared with the neat composite (S14). The linear stress–strain behaviour of the neat composite reflects its homogeneous nature and lacks
reinforcement compared to sample S1. SEM morphology shows evidence of non-uniform distribution of hybrid filler materials. In this case, the localized reinforcement zones were observed,
significantly increasing the strength. The filler materials occupied a few regions as filler clusters, which helped in delaying the early catastrophic failure due to the effective
redistribution of stress throughout the samples made with filler materials. The presence of Al2O3 and glass fibres formed regions with higher interfacial bonding, which helped compensate for
the weaker zones, resulting in an overall improvement in tensile strength. Similar findings were reported, where the synergetic interaction between fillers in certain regions improved the
mechanical performance. The filler materials with varied particle sizes, when not uniformly distributed, can lead to larger particles forming strong local reinforcement zones, while smaller
particles fill the gaps and enhance stress distribution and tensile strength. FRACTURE ANALYSIS USING SEM The SEM analysis was performed on the fractured regions of the samples post-tensile
test to understand the correlation of the ultimate tensile strength between the considered samples. Figure 14 illustrates the samples before and after the tensile test (the red circle
indicates the fracture region), and Fig. 15a,b show the sample preparation process for the tensile fracture analysis. Figure 16 shows the vertical placement of the samples in the analysis
setup. The SEM morphology of Sample S2 is shown in Fig. 17a–d. It was observed with voids, shallow voids, air pockets, alumina particle dispersion, particle agglomeration and fibre
breakages. The voids and air pockets are due to incomplete resin infiltration and inadequate curing at the marked region weakened the sample structure’s integrity. The addition of alumina
particles gets infused into the fibre matrix, which improves the hardness (6.39 Hv for S2 & 2.39 Hv for S14) of the sample, whereas the particle agglomeration due to uneven distribution
leads to poor load transfer between the matrix and fibres. These defects lead to fibre breakage when the composite is stressed beyond its limit. Sample S2 also observed a better UTS of 231
MPa compared to the neat composite (S14 -159 MPa), which indicates that the addition of two filler materials at an optimized level improves the ability to withstand higher stress than that
of neat composites. The SEM morphology of Sample S5 is shown in Fig. 18a–d. Sample S5 was observed to have fibres delaminated from the matrix element, fibre crack propagation, and breakage
near the regions of voids and air pockets, further weakening the structure, which diminishes the composites’ mechanical load-bearing capacity. Sample S5 (233 MPa, 6.99 Hv) and Sample S1 (236
MPa, 5.14 Hv) were observed with higher UTS and microhardness values compared to neat composite S14 (159 MPa, 2.39 Hv), which shows that the inclusion of single filler materials enhances
the overall strength of the composite by the better distribution of load before failure. The SEM morphology of Sample S6 is shown in Fig. 19a–f. Sample S6 was seen with voids, shallow voids,
fibre pullout, particle agglomeration, fibre fracture, fibre breakage and delamination. The Al2O3 particles observed to get embedded into the matrix (Fig. 19a) provided additional
reinforcement, leading to better stiffness and overall strength since the particles are hard and stiff26,27. The addition of two filler materials, Al2O3 and Mg particles, played as a barrier
to the crack propagation compared to neat composites’ delamination and fibre breakage. The presence of Al2O3 particles enhanced the interfacial bonding, which led to improved tensile
strength compared to neat composites since the neat composites’ bonding depends only on the resin matrix28. Sample S6 (229 MPa, 7.99 Hv) and Sample S2 (231 MPa, 6.39 Hv) were observed with
higher UTS and microhardness values compared to neat composite S14 (159 MPa, 2.39 Hv). The SEM morphology of Sample S11 is shown in Fig. 20a–f. It was observed with voids, shallow voids, air
pockets, collective regions of particle agglomeration and voids, fibre propagation, delamination, and fibre breakages. The sample was seen with particle agglomeration at various places and
more collectively in certain regions, resulting in non-uniform stress distribution and the clustered hybrid particles created weak zones, which led to the reduced tensile strength of the
sample (Fig. 20a,b,d,f). A collective region of voids was observed (Fig. 20f), and these voids reduced the overall integrity of the sample, which caused ease of crack initiation and
propagation. The poor bonding of fibres with the hybrid filler materials weakened the fibre-matrix bonding, resulting in reduced load-bearing and reduced tensile strength (S11, 144 MPa &
S14, 159 MPa). The combination of sample S11 might have exceeded the optimum volume fraction of the matrix, which led to filler-filler interactions rather than filler-matrix interactions.
The filler materials were not bonded well and were also observed to be at higher concentrations, creating more agglomeration regions and leading to premature failure at lower loads than
expected, which reduced the tensile strength of the sample. CUSTOM-BUILT TEST RIG DEFLECTION CHARACTERISTICS The deflection tests were carried out to explore the behaviour of composites with
and without GFRP sheets and with and without the presence of filler materials, and their results are shown in Table 8. Figure 21 shows the load versus deflection characteristics of the
tested samples D1–D4. The addition of Al2O3 as filler material makes the composite stiff with minimal deflection (sample D1) compared to other samples. The presence of Mg and Al2O3 makes the
composite sample less stiff due to insufficient fibre bonding (sample D2). It was observed that the addition of glass powder significantly reduced stiffness and made the sample more prone
to higher deflection (sample D3) due to non-uniform dispersion within the matrix and weakened in the localized regions. Using glass powder as filler material might improve the volume
fraction of the sample but may reduce the effectiveness of stress transfer between the fibres and matrix. It was also observed that the presence of a GFRP sheet confirms reduced deflection
compared to samples made with glass powder only (equivalent weight of the GFRP sheets were added to the samples as glass powder content, which is 22 g) due to the fibre matrix rigidity of
the fibre sheet. Therefore, the presence of GFRP sheets and filler materials (Al2O3 and glass powder) at the trade-off level increases the stiffness necessary to achieve low deflection at
specific load conditions and enhance the overall performance of composite materials. VERTICAL IRON IMPACTOR DROP WEIGHT TEST The influence of filler materials and fibre conditions was
assessed using a vertical iron impactor drop test set-up. As seen in Fig. 22, A1 is the composite sample prepared with 5%wt. Al2O3, 7.5%wt. Mg, and 6.5%wt. glass powder with GFRP as sheets;
B1 is the composite sample prepared with 5%wt. Al2O3, 0%wt. Mg, and 6.5%wt. glass powder with GFRP as sheets; C1 is the composite sample prepared with 5%wt. Al2O3, 7.5%wt. Mg; and 22 g of
glass powder (equivalent to the weight of the GFRP sheets) without GFRP as sheets; D1 is the composite sample prepared with 5%wt. Al2O3, 0%wt. Mg, and 22 g of glass powder without GFRP as
sheets; and 1 and 2 are numbers mentioned for before and after drop tests. It was observed that sample A has a lesser circular impact in the centre compared to sample B. Sample A shows
greater stiffness and resistance to deformation under the given load conditions with the addition of Mg powder, which was also confirmed in the deflection characteristics of sample D2 in the
custom-built test rig deflection characteristics. The presence of Mg powder enhances the impact absorption and helps in stress distribution, resulting in localized damage rather than
cracking for the sample made with GFRP sheets. It was also observed that sample C (with 7.5%wt. Mg and without GFRP as a sheet) was broken compared to sample D (with 0%wt. Mg and without
GFRP as a sheet). The total structure failure was observed for sample C due to the absence of the GFRP sheet, which leads to reduced stiffness and more shattering failure under impact.
Therefore, the optimal addition of Mg as filler material for GFRP-based composites is suggested for impact resistance applications. CONCLUSION The work explores the use of different filler
materials in the bidirectional glass fibre–reinforced polymer composites. The following are the observations made from this study: * 1. The addition of Mg and Al2O3 powders when used as
individual filler materials significantly improved the microhardness of the composites compared to the neat ones. In contrast, at high concentrations, it was observed that hybrid filler
materials (Mg and Al2O3) showed brittle phase formation, heterogeneity, and non-uniform distribution. Additionally, the presence of glass powder improved microhardness, whose inherent
hardness property aids in better reinforcement and interfacial bonding. * 2. The UTS was found to have more intricate results due to the variation in using three filler materials. Sample S1
with 5%wt. of Al2O3 powders and sample S5 5%wt. of Mg powders were seen with better strength (236 MPa and 233 MPa, respectively) compared to the neat composite (159 MPa). Further use of Mg
powder reduced the UTS of the composite samples due to the Mg-rich phase, which adversely led to a brittle phase, porosity, less load-bearing capacity, and weak interfacial bonding. The use
of Al2O3 improved the strength of the matrix up to its threshold usage (5%wt.); further increase in filler material concentration led to agglomeration in various regions, which weakened the
overall matrix strength. In contrast, it was observed that sample S7 with 5%wt. of Al2O3 powders and 5%wt. of Mg powders had reduced UTS (204 MPa). When a third filler material, glass
powder, was added at 6.5%wt. to the optimal double filler combination, the UTS drastically reduced to 149 MPa. Adding glass powder made the glass fibre matrix heterogeneous, leading to
premature failure with higher weak points and reduced interfacial bonding. * 3. The custom-built test rig deflection characteristics study showed that the presence of Al2O3 provided better
stiffness compared to the sample prepared with three filler materials. For applications requiring low deflection and better stiffness, an optimal addition of Al2O3 and glass powder in the
GFRP sheets is suggested. * 4. From the vertical iron impactor drop weight test, it was observed that the presence of Mg powder enhances the stiffness to resist deformation caused by
vertical iron impactor (sample A2). Even though the presence of Mg powder was found to be effective, it showed significant effects only in the presence of GFRP sheets. DATA AVAILABILITY The
datasets used and/or analysed during the current study available from the corresponding author on reasonable request. REFERENCES * Sharma, H. et al. Critical review on advancements on the
fibre-reinforced composites: Role of fibre/matrix modification on the performance of the fibrous composites. _J. Mater. Res. Technol._ 26, 2975–3002 (2023). Article CAS Google Scholar *
Vassilopoulos, A. P. The history of fibre-reinforced polymer composite laminate fatigue. _Int. J. Fatigue_ 134, 105512 (2020). Article CAS Google Scholar * Mishra, T., Mandal, P., Rout,
A. K. & Sahoo, D. A state-of-the-art review on potential applications of natural fibre-reinforced polymer composite filled with inorganic nanoparticle. _Compos. Part. C Open Access_ 9,
100298 (2022). Article CAS Google Scholar * Aisyah, H. A. et al. A comprehensive review on advanced sustainable woven natural fibre polymer composites. _Polymers_ 13, 471 (2021). Article
CAS PubMed PubMed Central Google Scholar * Shahabaz, S. M. et al. Effect of Al2O3 and SiC nano-fillers on the mechanical properties of carbon fibre-reinforced epoxy hybrid composites.
_J. Compos. Sci._ 7, 133 (2023). Article CAS Google Scholar * Kumar, K. N., Kumar, M. P., Krishna, V. & Rao, D. S. Experimental investigation on mechanical properties of coal ash
reinforced glass fiber polymer matrix composites. _Int. J. Emerg. Technol. Adv. Eng._ 3(8), 250–258 (2013). Google Scholar * Zhang, X., Yang, L., Wang, F. & Zhang, X. Effect of glass
bead content on the mechanical properties of polypropylene composites. _Mater. Des._ 69, 20–26 (2015). Google Scholar * Petersen, M. R., Chen, A., Roll, M., Jung, S. J. & Yossef, M.
Mechanical properties of fire-retardant glass fibre-reinforced polymer materials with alumina trihydrate filler. _Compos. Part. B Eng._ 78, 109–121 (2015). Article CAS Google Scholar *
Jian, Z., Wang, H., Li, H., Liu, Y. & Xiong, D. Preparation and characterization of glass bead/epoxy resin composites. _Polym. Compos._ 39, 3407–3413 (2018). Google Scholar * Reddy, M.
S. et al. Mechanical characterization of glass powder reinforced epoxy composites. _J. Reinf. Plast. Compos._ 39, 166–176 (2020). Google Scholar * Aveen, K. P., Bhajantri, V., D’Souza, R.
& Londe, N. V. Experimental analysis on effect of various fillers on mechanical properties of glass fibre reinforced polymer composites. _AIP Conf. Proc._ 2057, 020044 (2019). Article
Google Scholar * Buaphuen, P., Khunna, D. & Vittayakorn, W. Utilization of waste glass powder as a filler in epoxy resin based composite. _Integr. Ferroelectr._ 223, 58–67 (2022).
Article ADS CAS Google Scholar * Vijaya Rajan, V. & Gnanavel, B. K. An experimental investigation on enhancing the strength and stiffness of GFRP co-cured composite joint: Effect of
glass powder addition. _Mater. Res. Express_ 9, 8 (2022). Article Google Scholar * Zhang, T., Zhang, J., Zhao, Y. & Ai, H. Study on the performance and mechanism of glass
fibre-reinforced MgO-SiO2-H2O cement. _Materials_ 16, 6668 (2023). Article ADS CAS PubMed PubMed Central Google Scholar * Aryaswara, L. G., Kusni, M., Wijanarko, D. & Muflikhun, M.
A. Advanced properties and failure characteristics of hybrid GFRP-matrix thin laminates modified by micro glass powder filler for hard structure applications. _J. Eng. Res._ (In press)
(2023). * Zhang, Z. et al. Preparation and properties of Al2O3 modified epoxy-glass fibre composites. _Mater. Lett._ 370, 136832 (2024). Article CAS Google Scholar * Daffa Alandro, A. et
al. Comprehensive assessment of hybrid GFRP-graphite filler using modified complex Arcan fixture: Experimental and simulation approach. _Compos. Pt. A Appl. Sci. Manuf._ 180, 108094 (2024).
Article Google Scholar * Sriraman, N., Sreehari, V. M., Bharathi, R. J., Vinu, K. M. & Narayanan, N. S. Mechanical characteristics of glass epoxy composites with yttrium powder
fillers. _Mater. Today Proc._ 50(Part 5), 2462–2466. https://doi.org/10.1016/j.matpr.2021.10.363 (2022). Article CAS Google Scholar * Etika, K. C., Liu, L., Hess, L. A. & Grunlan, J.
C. The influence of synergistic stabilization of carbon black and clay on the electrical and mechanical properties of epoxy composites. _Carbon_ 47(12), 3128–3136.
https://doi.org/10.1016/j.carbon.2009.05.001 (2009). Article CAS Google Scholar * Uddin, M. F. & Sun, C. T. Improved dispersion and mechanical properties of hybrid nanocomposites.
_Compos. Sci. Technol._ 70(2), 223–230. https://doi.org/10.1016/j.compscitech.2009.10.001 (2010). Article CAS Google Scholar * Megahed, A. A., Agwa, M. A. & Megahed, M. Improvement of
hardness and wear resistance of glass fibre-reinforced epoxy composites by the incorporation of silica/carbon hybrid nanofillers. _Polym. Plast. Technol. Eng._ 57(4), 251–259.
https://doi.org/10.1080/03602559.2017.1320724 (2017). Article CAS Google Scholar * Megahed, M., Megahed, A. A. & Agwa, M. A. The influence of incorporation of silica and carbon
nanoparticles on the mechanical properties of hybrid glass fibre reinforced epoxy. _J. Ind. Text._ 49(2), 181–199. https://doi.org/10.1177/1528083718775978 (2019). Article CAS Google
Scholar * Alam, M. S. & Chowdhury, M. A. Characterization of epoxy composites reinforced with CaCO3-Al2O3-MgO-TiO2/CuO filler materials. _Alex. Eng. J._ (In press) (2020).
https://doi.org/10.1016/j.aej.2020.07.017 * Wan Badaruzzaman, W. H. et al. Mechanical properties and water absorption capacity of hybrid GFRP composites. _Polymers_. 14 (7), 1394.
https://doi.org/10.3390/polym14071394 (2022). Article CAS PubMed PubMed Central Google Scholar * Zamani, P., da Silva, L. F. M., Moghaddam, G., Masoudi Nejad, D., Soltannia, B. &
R., & Experimental study on mixing ratio effect of hybrid graphene nanoplatelet/nano-silica reinforcement on the static and fatigue life of aluminum-to-GFRP bonded joints under
four-point bending. _Compos. Struct._ 300, 116108. https://doi.org/10.1016/j.compstruct.2022.116108 (2022). Article CAS Google Scholar * El-Masry, M. M. & Imam, N. G. A comparative
study between Ag-CuO/epoxy and Mg-CuO/epoxy hybrid nanocomposites: Impressive electrical, mechanical, and thermal properties. _J. Mater. Res. Technol._ 18, 1784–1801.
https://doi.org/10.1016/j.jmrt.2022.03.039 (2022). Article CAS Google Scholar * Srinivasa Perumal, K. P., Selvarajan, L., Manikandan, K. P. & Velmurugan, C. Mechanical, tribological,
and surface morphological studies on the effects of hybrid ilmenite and silicon dioxide fillers on glass fibre reinforced epoxy composites. _J. Mech. Behav. Biomed. Mater._ 146, 106095.
https://doi.org/10.1016/j.jmbbm.2023.106095 (2023). Article CAS PubMed Google Scholar * Kumara, R., Bairwa, K. N. & Reddy, D. R. Influence of addition of Al2O3 and SiC on tensile and
flexural characteristics of epoxy/glass fibre hybrid polymer composite. _Mater. Today Proc._ (In press). * Kose, H., Bayar, I. & Ergün, R. K. Experimental optimization of CuO and MgO
hybrid nanoparticle reinforcement ratios to enhance fatigue life of GFRP composites. _Polym. Compos._ 45(3). https://doi.org/10.1002/pc.28536 (2024). Download references ACKNOWLEDGEMENTS The
authors acknowledge the aid from the “Advanced Composites for Aerospace Applications Lab Facility” at SASTRA Deemed University through the support of Prof. TRR’s fund for sample
preparations. They also thank SASTRA Deemed University for granting permission to use the vertical iron impactor drop weight test and custom-built deflection test rig. The authors are also
grateful to the National Institute of Technology, Tiruchirappalli, for providing access to the universal testing machine and to the National College, Tiruchirappalli, for the SEM and EDAX
facility and to DST-FIST & ACIC, St. Joseph’s College, Tiruchirappalli for the SEM facility. AUTHOR INFORMATION AUTHORS AND AFFILIATIONS * School of Mechanical Engineering, SASTRA Deemed
University, Thanjavur, Tamil Nadu, India N. Sathiya Narayanan, D. Sai Venkat Mohan, Javvadi Abhinay, Torlapati Dinesh, Veerla Satya Sai Surya Teja & Rajanala Praneeth Authors * N.
Sathiya Narayanan View author publications You can also search for this author inPubMed Google Scholar * D. Sai Venkat Mohan View author publications You can also search for this author
inPubMed Google Scholar * Javvadi Abhinay View author publications You can also search for this author inPubMed Google Scholar * Torlapati Dinesh View author publications You can also search
for this author inPubMed Google Scholar * Veerla Satya Sai Surya Teja View author publications You can also search for this author inPubMed Google Scholar * Rajanala Praneeth View author
publications You can also search for this author inPubMed Google Scholar CONTRIBUTIONS N.S.N., as the corresponding author, worked on the methodology and manuscript draft; D.S.V.M. and J.A.
prepared the samples and performed required tests; V.S.S.S.T., R.P. and T.D. prepared another set of samples and conducted required testing. All authors have reviewed the manuscript.
CORRESPONDING AUTHOR Correspondence to N. Sathiya Narayanan. ETHICS DECLARATIONS COMPETING INTERESTS The authors declare no competing interests. ADDITIONAL INFORMATION PUBLISHER’S NOTE
Springer Nature remains neutral with regard to jurisdictional claims in published maps and institutional affiliations. RIGHTS AND PERMISSIONS OPEN ACCESS This article is licensed under a
Creative Commons Attribution-NonCommercial-NoDerivatives 4.0 International License, which permits any non-commercial use, sharing, distribution and reproduction in any medium or format, as
long as you give appropriate credit to the original author(s) and the source, provide a link to the Creative Commons licence, and indicate if you modified the licensed material. You do not
have permission under this licence to share adapted material derived from this article or parts of it. The images or other third party material in this article are included in the article’s
Creative Commons licence, unless indicated otherwise in a credit line to the material. If material is not included in the article’s Creative Commons licence and your intended use is not
permitted by statutory regulation or exceeds the permitted use, you will need to obtain permission directly from the copyright holder. To view a copy of this licence, visit
http://creativecommons.org/licenses/by-nc-nd/4.0/. Reprints and permissions ABOUT THIS ARTICLE CITE THIS ARTICLE Sathiya Narayanan, N., Sai Venkat Mohan, D., Abhinay, J. _et al._ Effects on
microhardness, tensile strength, deflection, and drop weight impact resistance with the addition of hybrid filler materials for enhancing GFRP composites. _Sci Rep_ 14, 27524 (2024).
https://doi.org/10.1038/s41598-024-76094-6 Download citation * Received: 17 July 2024 * Accepted: 10 October 2024 * Published: 11 November 2024 * DOI:
https://doi.org/10.1038/s41598-024-76094-6 SHARE THIS ARTICLE Anyone you share the following link with will be able to read this content: Get shareable link Sorry, a shareable link is not
currently available for this article. Copy to clipboard Provided by the Springer Nature SharedIt content-sharing initiative KEYWORDS * Hybrid composites * Aluminium oxide * Magnesium *
Filler materials * Structural applications